top of page
COPPER ON ALUMINUM
Copper and aluminum are almost impossible to weld. They undergo a chemical reaction and form intermetallic phases when they come into contact with each other. This reaction is enhanced when electrical current passes between them, and in the presence of moisture or high temperatures. This produces a brittle and non-conductive phase at the interface between the two metals. For this reason, copper and aluminum electrical contacts do not make good partners. However, since these metals are such good conductors, there are many electrical applications where they unavoidably come into contact with each other.
There are some methods such as friction welding that do weld copper and aluminum, but they all rely on high temperatures. This is a problem. Conventional explosive welding can be used to weld copper to aluminum without heat, but the process causes waves at the interface. These waves experience high temperatures for an instant, caused by the movement of metal as the waves are being formed, and this creates intermetallics within the waves. The presence of these intermetallic phases interferes with conductivity.
Sigmabond's process produces a waveless interface, completely avoiding intermetallic phases. The result is a stronger and more conductive bond between the two metals. This material is perfect for making electrical connections between copper and aluminum.
Conventional: has AL2CU intermetallic phases
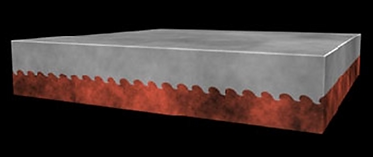

Al
Cu
Al Cu intermetallic region
2
Sigmabond: eliminates waves and intermetallic phases


Cu
Al
No intermetallics
SELECTED PUBLICATIONS
Ref. Fan Y., Sinclair A., Masterson C., Mikhani K., Sildva H. & Szecket A. (2003). Ultrasonic Characterization of the Interfacial Zone in a Copper/Aluminum Explosive Weld. Materials Evaluation. [article]
bottom of page