TITANIUM CLADDING: A BETTER PROCESS
STRONGER / FASTER / CHEAPER
CONVENTIONAL PROCESS
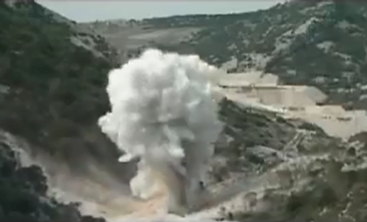
The conventional process for making titanium clad plate today is large and cumbersome. An example of the scale of operations in a typical explosive welding facility can be seen in a video by Dynamic Materials Corporation (DMC), where they showcase their production methods. This gives a good explanation of the challenges faced by any explosive welding producer.
DMC is among the best in the business and is the market leader in North America for the supply of titanium clad plate. With the conventional process, this is as good as it gets.
Check out their video at the link below.
Sigmabond's research team tore through the conventional practices, one element at a time, until the quantum leap occurred. Our advanced new process is now easier, faster and cheaper, as it brings everything into the most optimum conditions for explosive welding.
This means we produce only small clads that are easy to make, and at the most optimum parameters where everything is perfect. At this stage, we think only about ourselves. We are only interested in producing the best explosive weld possible, without regard for the end product. This allows to make a perfect clad. We then use roll bonding technology to produce, from this perfect small clad, the large finished clad material for the customer. It is at this second stage where we focus on the client's needs. The much easier and more foregiving roll bonding process is used to tailor the finished clad to the exacting details of the customer's requirements. So, we are combining the best of both technologies to get the best of both worlds. This is a first for the industry.
Roll bonding gives us powerful leverage. Every explosively welded clad plate we make produces 100 to 200 times its area in final clad material for the customer.

SIGMABOND'S NEW IMPROVED PROCESS
OUR PROCESS
-
Our process is standardized to one small easy-to-use production size
-
All materials and dimensions are always maintained at their “sweet spot”
-
We take advantage of roll bonding, a high volume process that enables low cost production of very large clad plates
-
We can stockpile our standard explosively welded clads to save time when filling customer orders
-
No need for post-bond flattening
-
No need for an anvil
THE RESULT
-
Lower production cost (cost advantage increases with thinner clads)
-
Ability to produce large plate sizes and thin clad layers
-
Fast turnaround (weeks instead of months)
-
Reproducibility and quality control in the explosion bonding process, unprecedented in the industry
-
Titanium clad material not affected by high temperatures, enabling the roll bonding process
-
Explosive loading is lighter
-
Ability to use any grade of titanium, or zirconium
-
Almost no edge effects or material losses
-
Stronger, more consistent bond strength

Conventional method is always struggling at the outside edges of the technology.

Sigmabond method is always in the sweet spot of explosive welding.
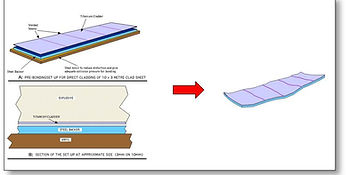
Conventional method is limited to one finished plate per explosion

Conventional method requires large production sizes for explosive welding.

Conventional method requires extensive preparation.

Sigmabond method leverages roll bonding with explosive welding to multiply yield
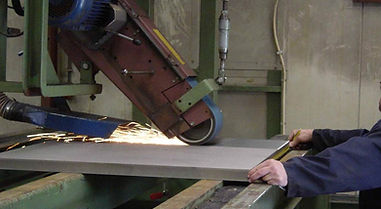
Sigmabond method uses a small, light, easy-to-use production format for explosive welding.

Sigmabond method takes advantage of roll bonding, a high volume process.

Conventional method can be cumbersome and sometimes bonding is not fully successful.
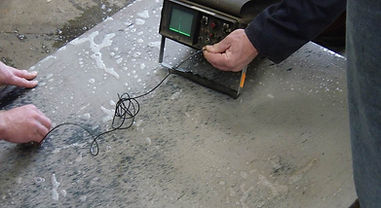
Sigmabond method is less cumbersome and bonding errors are virtually eliminated.
SELECTED PUBLICATIONS
Ref. Hardwick R. (2005). A new titanium and zirconium clad plate: A breakthrough in cladding technology. Welding & Cutting; Volume 4, No. 3 [article]